Salt spray: how to protect marine electronics from salt, salt fog, corrosion?
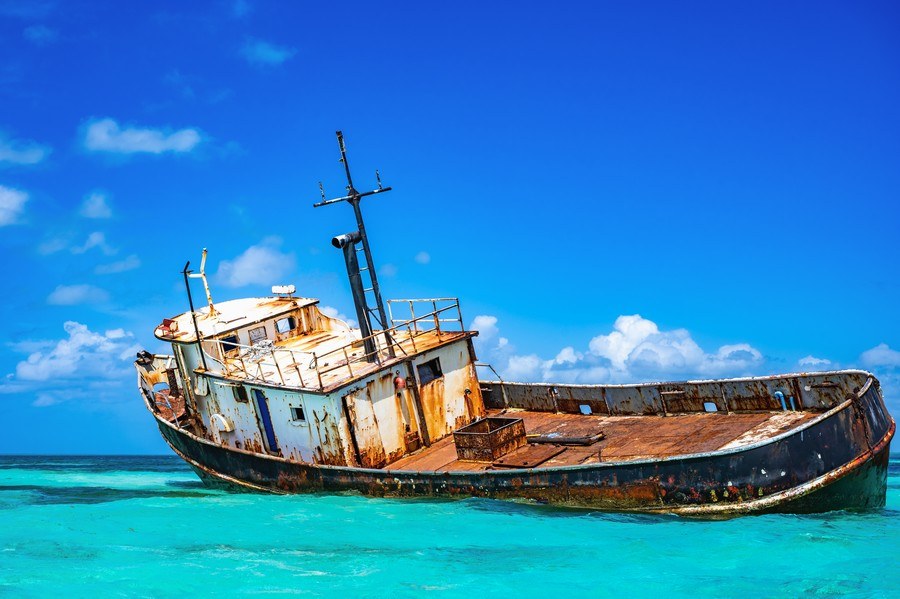
Protecting marine electronics from corrosion requires tests to distinguish and understand the causes of degradation and evaluate the protection solution. To prevent corrosion and protect electronics, there is a particularly effective test: the salt spray test. Carried out in a corrosion chamber, these tests are designed to validate the resistance over time of the various elements on board.
Corrosion on ships: why is it important to protect electronic equipment?
The real danger with marine electronics and exposure to saltwater is that it doesn’t take a lot of salt residue to cause great damage in sensitive circuitry. While fully immersion of an electronics component in saltwater will most certainly cause shorts and rapid corrosion of any protective sealants, even a small amount of salt residue carried through salt fog or salt spray will likely damage equipment over time.
Corrosion and rusting. Salt water or spray contains the chemical NaCl, or sodium chloride. It acts like a charged ion when it is separated by water so it can pull your electricity from different surface materials that typically do not conduct electricity. This is all due to chemical bonding. The phenomenon of corrosion occurs through a chemical-physical interaction between a metallic material and its environment or other materials surrounding it. When salt water or salt spray comes into contact with an electronic equipment, it can badly corrode the protection surface of printed circuit board. Overtime the electrical connections will also corrode creating faults. To prevent this corrosion phenomenon from occurring, especially in marine atmospheres, it is crucial to optimize the choice of materials and their organic or inorganic coating.
How to protect electronic installed on boat ?
Enclosures: They are the standard way to protect electronics from dust and moisture ingress. Hundreds of enclosure are available for power electronics offering up to IP68 rating. Of course they can be manufacture in shape of any size using metallic or plastic materials.
Conformal coating: They are available in solvent-based, water-based and 100% active materials and are deposited on the surface of the PCB as a protective 25-75µm thick film. Various types of products are available for wide range of characteristics (application process, use, temperature, dielectric, water…)
Potting resin: It’s a process of filling the complete electronic assembly PCB with an resin. It offers a better adhesion, high temperature and chemical resistance. Resin are available in epoxy, polyurethane or silicone materials. Each family of chemistry has strengths and weaknesses and offers a variety viscosities, hardness application and cure conditions.
What tests should be carried out to ensure the corrosion resistance of the electronics?
Corrosion or salt spray tests are often carried out in an artificial atmosphere, in order to analyze the performance of the part or system under test. Condensation, immersion or salt spray tests, there are many types of tests which can sometimes be combined and alternated. The test(s) to be performed should be chosen according to the item to be tested, its properties and characteristics. For electronic components, it is possible to carry out a salt spray test.
Neutral or acetic salt spray tests to protect ship electronics from corrosion
Salt spray tests are used to check the resistance of a metallic material, with or without a protective coating, to corrosion.
The neutral salt spray test, also known as the NSS (Neutral Salt Spray) test, is very effective in detecting changes in certain organic, metallic, conversion layer or anodic oxide coatings. The duration of the test varies according to the materials to be tested and can reach more than 1,000 hours for those particularly resistant to corrosion.
The acetic or copper-acetic salt spray test, also known as the ASSS (Acetic Acid Salt Spray) test or the CASS (Copper Accelerated Salt Spray) test, is more commonly used to test the resistance of decorative coatings made from a mixture of copper, nickel or chromium, as well as organic or anodic coatings on aluminum alloys.
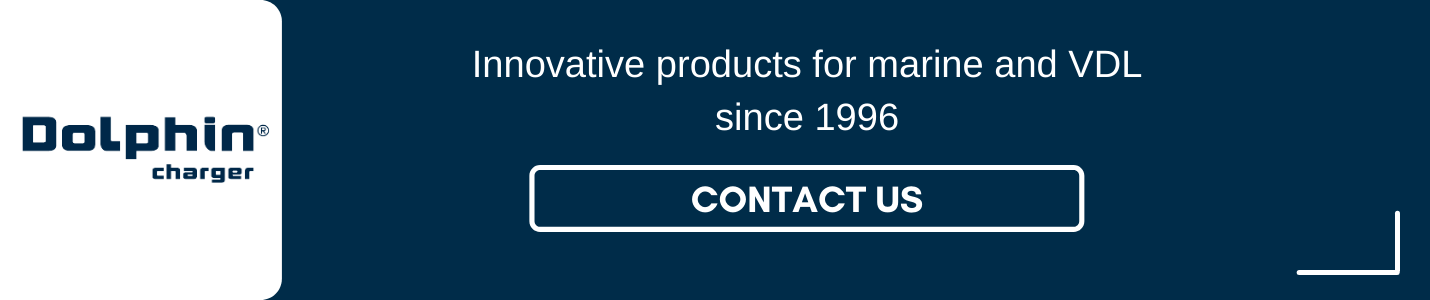
What are the salt spray test conditions?
The methodology and procedures for neutral or acetic salt spray testing are governed by DO-160, ISO 9227, ASTM B117 and ISO 60068. To validate the results obtained, the tests must be carried out in strict compliance with these standards. In particular, there are density, pH and rainfall controls to be carried out during the test. Duration of tests may varies from 2h till 1 000h.
How to interpret the results of the salt spray test?
Following a salt spray test, the nature of the corrosion should be qualified and the degradation of the different materials compared. This can be done in different ways:
By weighing the elements tested before and after the test: significant corrosion leads to weight gain (change in mass).
By carrying out micrographic examinations on sections, in order to determine the depth of the corrosion.
By comparing photos of the corroded elements taken during the salt spray test to illustrate the corrosion phenomena and their evolution over time.
In the marine field, being on the water brings with it corrosion issues that are important to be fully protect, especially when it comes to protecting the electronics on board boats. Dolphin Charger® , the marine specialist, offers battery charging solutions specially designed to resist corrosion: Dolphin charging PCB’s are tested and treated against salt spray. Tropicalized and marine grade , our products have a protective varnish that will make the electronics last over time! Would you like to know more? Contact us for more information!